Srovnání konečných vlastností portlandských cementů vlivem druhu mletí
Název portlandský cement byl odvozen od vzhledu betonu, který se podobal pískovci, jež se nacházel u anglického města Portland. V roce 1824 byl Johnu Aspdinovi udělen patent na výrobu portlandského cementu. Jedním z klíčových kroků ve výrobním procesu cementu je mletí. Tradiční mletí v trojkomorovém mlýně je časově a energeticky náročné. Příspěvek je věnován alternativnímu způsobu mletí, kterým je vysokorychlostní mletí s cílem redukce mlecího času a energie. Výsledky ukazují, že se zkrácenou dobou mletí, potřebnou k dosažení stejného měrného povrchu, dochází k snížení spotřeby elektrické energie. Efekt mechanochemické aktivace má malý vliv na hydrataci cementu. Největší přínos této technologie je redukce spotřebované elektrické energie při zachování srovnatelných technologických vlastností.
Úvod
Před uskladněním v krytých halách dochází k předrcení slinku na částice o velikosti 5 až 10 mm. Drcení probíhá v kuželovém nebo odrazovém drtiči. Následné odložení trvá okolo tří týdnů. Slinek je dopravován do mlýnice spolu se sádrovcem nebo jinými přísadami, kde se mele na požadovanou jemnost [1, 2].
Mlýn pro mletí slinku je většinou komorový kulový mlýn. Důležité je správné plnění mlecími tělesy a surovinou. Dále se používají mlýny oběhové, ve kterých se mele na uzavřený okruh a výmel je tříděn ve větrném třídiči a nedomleté částice se vracejí zpět do mlýna, kde se dále melou. Oběh meliva je obstaráván mechanicky nebo pneumaticky [1]. Mletí je energeticky náročný proces. Na 1 tunu cementu je potřeba 20–30 kWh. Pro snížení spotřeby energie se do cementu přidávají aktivátory mletí. Tyto látky spoří energii až o 35 %. Na mletí slinku se sádrovcem se spotřebuje přibližně 1 % energie, zbytek se přemění na teplo. Účinnost mletí se udává v desetinách procenta. Dochází k výraznému ohřevu cementu, a to až na 180 °C. Cement v mlýnici je chlazen proudem vzduchu, který zároveň odvádí páry vzniklé rozpadem sádrovce. Nejvhodnější velikost částic je 5–35 μm. S rostoucí jemností meliva se zvyšuje množství spotřebované energie a výkon mlýna značně klesá. Tato skutečnost je způsobena vzrůstajícím odporem meliva při pokračujícím rozpojování částic [4, 5]. Mechano-chemická aktivace se zabývá fyzikálně-chemickými změnami v látkách ve všech stavech agregace vlivem mechanické energie [3, 6]. Výhodami této technologie je snížení reakční teploty materiálu, zvýšení reaktivity materiálů, zkrácení doby mletí (snížení energetické náročnosti) a snížení počtu technologických stupňů.
Použité materiály a metody
Jako výchozí suroviny pro přípravu portlandského cementu byly zvoleny slinek z cementárny Mokrá a chemosádrovec z Prechezy a.s. Přerov, jenž se vyznačuje vysokou čistotou a bílou barvou. Jako referenční vzorek byl zvolen cement CEM I 42.5 R z produkce cementárny Mokrá. Následně byly základní suroviny dostatečně homogenizovány po dobu 24 hod. Po homogenizaci byly uloženy do laboratorního kulového mlýna (BRIO OM 20), kde se předemlely na výchozí měrný povrch 300 m2/kg. Takto připravený vzorek byl rozdělen do dvou šarží. První šarže byla pomleta vysokorychlostním kolíkovým mlýnem – desintegrátorem DESI osazeném rotory SR PV. Následně byla zjištěna hodnota měrného povrchu. Měrný povrch byl měřen za pomoci přístroje PC-Blaine-Star s objemem komory 7,95 cm3.
Druhá šarže byla pomleta na odpovídající měrný povrch, tj. 380 kg/m2, pomocí kulového mlýna. Morfologie zrn byla stanovena pomocí skenovací elektronový mikroskopie SEM. Použit byl přístroj Tescan MIRA 3 XMU s detektorem sekundárních elektronů. Distribuce částic byla určena pomocí laserového granulometru Malvern Mastersizer 2000 ve vzdušném disperzním prostředí. Mineralogické složení po 7 a 28 dnech hydratace bylo určeno rentgenové difrakce REM. Použitým přístrojem byl XRD Empyrean. Pomocí diferenčně termické analýzy DTA analýzy bylo určeno množství CaO, použitým přístrojem byl Mettler Toledo TGA/DSC 1. Hodnoty pevností v tahu za ohybu a v tlaku při stáří vzorku 7 a 28 dní byly stanoveny na zkušebním lise s rozsahem do 3000 kN.
Naměřené výsledky
Portlandský slinek, odebraný z cementárny Mokrá a chemosádrovec z Prechezy Přerov a.s. byly podrobeny chemické analýze, výsledky jsou zaznamenány v tabulkách 1 a 2. Jako referenční vzorek byl zvolen CEM I 42.5 R, hodnoty z chemické analýzy jsou uvedeny v tabulce č. 3.
Složka | CaO | MgO | SiO2 | Al2O3 | Na2O | Fe2O | TiO2 | P2O5 | Ostatní |
---|---|---|---|---|---|---|---|---|---|
Obsah [%] | 64,0 | 1,60 | 23,20 | 4,80 | 0,60 | 2,40 | 0,30 | 0,20 | 2,90 |
Složka | CaSO4∙2 H2O | H2O | CaSO4 | Ostatní |
---|---|---|---|---|
Obsah [%] | 84,00 | 11,00 | 2,40 | 2,60 |
Složka | CaO | SiO2 | Al2O3 | Fe2O | K2O | MgO | Na2O | TiO2 | SO3 | Ostatní |
---|---|---|---|---|---|---|---|---|---|---|
Obsah [%] | 64,91 | 20,26 | 5,92 | 5,18 | 1,75 | 1,14 | 0,3 | 0,21 | 0,20 | 0,13 |
Po dostatečné homogenizaci byly suroviny uloženy do laboratorního kulového mlýna, kde se mlely na výchozí měrný povrch tj. 300 m2/kg po dobu 90 minut. Takto připravená surovina byla rozdělena na dvě poloviny. První polovina byla pomleta vysokorychlostním rotorovým mlýnem (Dezintegrátor), druhá polovina byla pomleta pomocí kulového mlýna (Kulový mlýn). Z takto připraveného cementu se odebraly vzorky na stanovení měrného povrchu pomocí Blainova přístroje. Hodnoty jsou zaznamenány v tabulce č. 4 spolu s hodnotami referenčního vzorku CEM I 42.5R Mokrá (Reference).
Vzorek | Povrch [m2/kg] |
---|---|
Reference | 391 |
Dezintegrátor | 386 |
Kulový mlýn | 383 |
Elektronovým mikroskopem byla sledována velikost a tvar částic. Pro porovnání byly vybrány snímky s 600× zvětšením. Snímky z elektronového mikroskopu jsou zobrazeny na obrázcích 1 až 3.
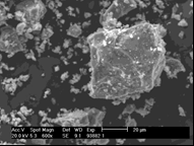
Obr. č. 1: kulový mlýn (300) – 600× zvětšení
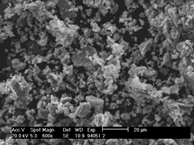
Obr. č. 2: dezintegrátor (386) – 600× zvětšení
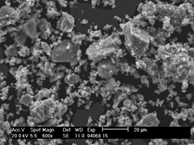
Obr. č. 3: kulový mlýn (383) – 600× zvětšení
Z mikroskopických snímků je patrné, že při domletí došlo ke značnému zmenšení zrn. Částice mleté v dezintegrátoru i v kulovém mlýně mají krychlový až kulovitý tvar. Účinnost obou mletí je srovnatelná.
Křivka zrnitosti byla stanovena pomocí laserového granulometru. Distribuce částic je zobrazena v grafech 1 až 3.
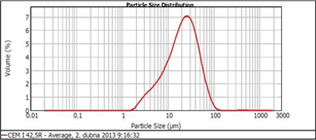
Graf č. 1 – granulometrické rozložení – reference
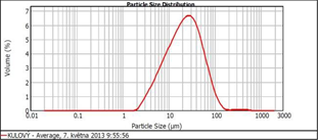
Graf č. 2 – granulometrické rozložení – kulový mlýn
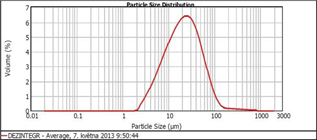
Graf č. 3 – granulometrické rozložení – dezintegrátor
Z grafů je patrné, že průběh granulometrie je u kulového mlýnu i u dezintegrátoru prakticky stejný. Oba typy mletí vedly ke snížení hrubých částic oproti referenci.
Pomocí RTG analýzy byl sledován hydratační proces u vzorků mletých na kulovém mlýně a dezintegrátoru ve stáří 7 a 28 dní. Výsledky jednotlivých měření jsou znázorněny v příslušných výstupních grafech č. 4 až 6.
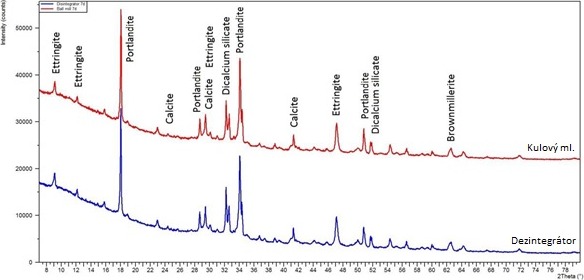
Graf č. 4 – XRD 7denní hydratace
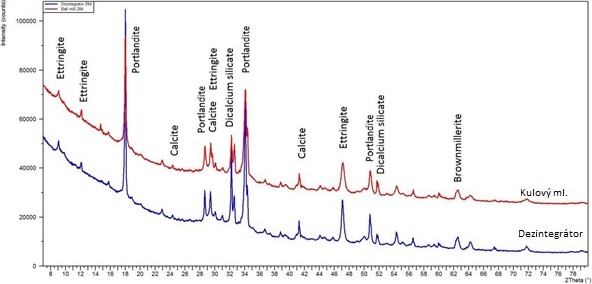
Graf č. 5 – XRD 28denní hydratace
Z rentgenogramu při 7denním zrání jsou patrné shodné velikosti píku jednotlivých minerálů. U vzorků z 28denního zrání je na detail píku viditelný větší podíl portlanditu u vzorku mletém na vysokorychlostním dezintegrátoru. Tato skutečnost může indikovat vyšší reaktivnost vzorku a zlepšení fyzikálně-mechanických vlastností.
Z DTA analýzy bylo vypočteno množství CaO. Příslušné hodnoty jsou uvedeny v tab. 5.
Vzorek | Množství CaO [%] | |
---|---|---|
7denní | 28denní | |
Kulový mlýn | 14,187 | 16,911 |
Dezintegrátor | 16,509 | 17,237 |
Reference | – | 18,329 |
Z vypočtených hodnot je patrné, že nejvyšší obsah CaO při 28denním zrání má komerčně vyráběný cement. Nejnižší hodnota byla zjištěna u vzorku mletém na kulovém mlýně. Vyšší hodnotu obsahu CaO u vzorku mletém v dezintegrátoru může mít za následek mechano-chemicky aktivovaný povrch.
Na jednotlivých vzorcích byly sledovány fyzikálně-mechanické vlastnosti. Hodnoty pevností v tahu za ohybu a v tlaku jsou uvedeny v tabulkách č. 6 a 7.
Vzorek | Rf [MPa] | |||
---|---|---|---|---|
1. den | 3. den | 7. den | 28. den | |
Reference | 2,29 | 4,52 | 5,12 | 5,56 |
Kulový mlýn | 4,23 | 7,00 | 8,03 | 8,13 |
Dezintegrátor | 4,52 | 6,20 | 8,20 | 9,34 |
Vzorek | Rf [MPa] | |||
---|---|---|---|---|
1. den | 3. den | 7. den | 28. den | |
Reference | 11,8 | 27,7 | 38,7 | 44,9 |
Kulový mlýn | 14,0 | 26,7 | 36,3 | 45,8 |
Dezintegrátor | 13,9 | 24,4 | 35,5 | 45,9 |
Z naměřených hodnot je patrné, že druh mletí neměl zásadní vliv na vývoj pevností. Časová a energetická náročnost jednotlivých mletí jsou zahrnuta v tabulce č. 8.
Vzorek | Doba mletí [min] | Spotřeba energie [kWh] |
---|---|---|
Mletí na povrch 300 m2‧kg−1 | ||
Kulový mlýn (300) | 90 | 6,00 |
Dodatečné mletí na finální měrný povrch | ||
Kulový mlýn (383) | 40 | 2,67 |
Dezintegrátor (386) | 5 | 0,42 |
Kombinované hodnoty | ||
Kulový mlýn (383) | 130 | 8,67 |
Dezintegrátor (386) | 95 | 6,42 |
Z výsledků je zřejmé, že časová i energetická náročnost je při mletí v dezintegrátoru výrazně nižší.
Diskuze výsledků
Výchozí suroviny byly předemlety pomocí kulového mlýna na měrný povrch 300 m2/kg. Takto předpřipravená surovina byla rozdělena na dvě poloviny. První část byla domleta na vysokorychlostním dezintegrátoru a druhá pomocí kulového mlýna na srovnatelný měrný povrch. Jako reference byl použit komerčně vyráběný CEM I 42.5 R, u kterého se rovněž stanovil měrný povrch pomocí Blainova přístroje.
REM analýza prokázala, že použitím dezintegrátoru bylo dosaženo prakticky shodné granulometrie jako u vzorku mletého na kulovém mlýně. Zrna byla kubického tvaru, rovnoměrně namletá, bez vyššího obsahu hrubých částic.
Z křivek zrnitosti získaných z laserového granulometru je patrné, že při mletí na kulovém mlýně a pomocí dezintegrátoru došlo k rovnoměrnějšímu namletí vzorku oproti komerčně vyráběnému cementu.
Po provedení RTG analýzy je zřejmé, že hydratační proces probíhá u obou vzorků identicky. Pouze u vzorku mletého na dezintegrátoru byly po 28 dnech zrání pozorovány vyšší bazální linie portlanditu. Tento jev je patrně způsoben rovnoměrnějším namletím a vede ke zvýšení reaktivnosti.
Pomocí DTA analýzy se stanovil obsah CaO v jednotlivých vzorcích po 7 a 28 dnech zrání. Po 7 dnech byl u vzorku mletého na kulovém mlýně pozorován nižší obsah CaO ve srovnání se vzorkem připraveným pomocí dezintegrátoru. Tato skutečnost může být způsobena nižší reaktivitou vzorku. Při 28denním zrání byl obsah CaO takřka srovnatelný. Vzorek mletý v dezintegrátoru měl celkově vyšší obsah CaO. Tato skutečnost může indikovat celkově vyšší reaktivnost vzorku a zlepšení fyzikálně-mechanických vlastností, zejména pevnosti.
Ze stanovení fyzikálně-mechanických vlastností je patrné, že technologie mletí má minimální vliv na pevnosti v tlaku. Nejnižších pevností v tahu za ohybu dosahoval komerčně vyráběný vzorek cementu.
Největší rozdíl byl v mlecím čase a spotřebované energii. Při mletí na srovnatelný povrch, vysokorychlostní dezintegrátor ukazuje výhody vůči kulovému mlýnu, a to z časového i energetického hlediska. Finální vlastnosti cementu přitom zůstávají stejné.
Závěr
Jednou z možností, jak snížit energetickou náročnost mletí je využití mechano-chemické aktivace pomocí vysokorychlostního dezintegrátoru. Důvodem, proč nebylo této technologie hojně využíváno v minulosti je složitá konstrukce mlýnů a nesnadná údržba. V současné době, díky využití otěruvzdorných materiálů, se zvyšuje životnost mlecích těles.
Z výsledků provedených zkoušek plyne, že použitím dezintegrátoru lze vyrobit cement, který má stejné vlastnosti jako komerčně vyráběný. Největším přínosem je významná úspora energie, díky zkrácené době mletí.
Předpokladem perspektivního využití je výroba směsných cementů. Použití této metody je však potřeba hlouběji prozkoumat. Další výzkum by měl být zaměřen na využití různých tvarů rotorů, jejich kombinace, případně využití intenzifikátorů mletí.
Poděkování
Práce byla realizována v rámci řešení projektu č. LO1408 „AdMaS UP – Pokročilé stavební materiály, konstrukce a technologie“ podporovaného Ministerstvem školství, mládeže a tělovýchovy v rámci účelové podpory programu „Národní program udržitelnosti I“ a projektu číslo 15–08755 S „Studie vlivu přípravy vzorků na výsledné vlastnosti anorganických pojiv“.
Použitá literatura
- SCHORCHT, F; KOURTI, I; SCALET, B; ROUDIER, S; SANCHO, L; Best Available Techniques (BAT) Reference Document for the Production of Cement, Lime and Magnesium Oxide. 2013, DOI: 10.2788/12850
- KEPPERT, M., REITERMAN, P., PAVLÍK, Z., PAVLÍKOVÁ, M., JERMAN, M., ČERNÝ, R., Municipal solid waste incineration ashes and their potential for partial replacement of Portland cement and fine aggregates in concrete. Cement Wapno Beton. 2010, vol. 15/77, no. 4, p. 187–193. ISSN 1425-8129.
- DVOŘÁK, K.; FRIDRICHOVÁ, M.; DOBROVOLNÝ, P. Influence of different grinding types on granulometry of recycled glass. In Construction Materials and Structures. Jihoafrická republika, IOS Press. 2014. p. 305–310. ISBN 978-1-61499-465-7
- BOND, F.C.; Crushing and grinding calculations Part I, British Chemical Engineering 6 (1961) 378–385
- BOND, F.C.; Crushing and grinding calculations Part II, British Chemical Engineering 6 (1961) 543–634
- BALÁŽ P., Mechanochemistry in Nanoscience and Minerals Engineering, 2008, Springer- Verlag Berlin Heidelberg, 414 p.
- Hanykýř, V., Kutzendörfer, J.: Technologie keramiky, 2000, Silis
V současné době patří ekonomické aspekty k důležitým a mnohdy i k rozhodujícím faktorům nejrůznějších technologických procesů. U energeticky náročné výroby portlandského cementu se tak jedná o téma velice aktuální. Tento příspěvek se zabývá studiem vlivu způsobu mletí finálních složek portlandského cementu na jeho vlastnosti. Požitá metodika reflektuje bohaté zkušenosti a technické zázemí autorského kolektivu. Prezentované výsledky jsou velice přínosné a mohly by zásadně přispět ke zvýšení energetické efektivity výroby cementu. Při navazujícím výzkumu by bylo vhodné experimentální program doplnit o studium vlivu na reologii čerstvých past cementů připravených v různých režimech mletí.
The name of Portland cement was derived from tie appearance of concrete, which resembled sandstone located near the English city of Portland. In 1824, John Aspdin was granted a patent to produce Portland cement. One of the key steps in cement production is milling. Conventional milling method in three chamber mill has high time and energy requirements This paper deals with the possibility of usage of alternative grinding method, specifically using high speed pin mill in other to reduce time and energy consumption. Results show that because of reduced time of grinding needed to achieve comparable specific surface area, reduction of needed energy occurs. The effect of mechanochemical activation has small effect on cement hydration. The greatest benefit is the reduction of energy needed for grinding while maintaining the properties of the resulting cement.