Analýza stávajícího stavu jako východisko predikce další životnosti střešního pláště ploché střechy
V expertní oblasti nebo znalecké oblasti je obvyklým požadavkem nalezení případné poruchy, její příčiny a návrh způsobu jejího odstranění. Stále častěji se v expertní praxi však setkávám s požadavkem současně posoudit stávající stav ploché střechy a zejména hydroizolační vrstvy a vyjádřit se k její možné další funkčnosti a životnosti.
1.Úvod
Vzhledem k vývoji technologií zaujaly v 21. století v oblasti hydroizolací plochých střech jednoznačně dominantní místo hydroizolační fólie. O jejich druzích, vlastnostech, zkoušení a technologiích provádění existuje široká škála informačních podkladů, pro zájemce bych doporučil výborný podklad zpracovaný Technickou komisí pro hydroizolační fólie z.s. [1].
Zájemce tam získá skutečně komplexní přehled o celé problematice technologie výroby a aplikace hydroizolačních fólií. Pro ověřování vlastností v rámci uvádění výrobků na trh platí jasná pravidla a předepsané normativní postupy, které mají svůj jasný věcný účel a technický rámec.
2. Posuzování vad a poruch stávající skladby
Jinak je tomu ale v případě posuzování vad, poruch a vlastností hydroizolačních fólií v etapě jejich užívání. Pro tuto problematiku jasná pravidla nejsou jednoznačně dána a pokud nejde o zadání znaleckého posudku soudem s konkrétně určenými otázkami, pak každý expert nebo znalec může volit své postupy, které uzná pro daný úkol za vhodné. A již vůbec neexistuje jednotné východisko pro predikci další možné životnosti stávající střechy posuzované z hlediska jejich vad, poruch a způsobu jejich odstranění.
Vzhledem k výraznému zájmu majitelů a uživatelů plochých střech právě o vyjádření k možné další životnosti na základě zjištění stávajícího stavu jsem vytvořil vlastní metodiku, sestávající z následujících kroků:
- Vizuální prohlídka s posouzením všech detailů
- V případě střechy s přístupnou hydroizolační vrstvou mechanické prověření svarů
- Vlhkostní průzkum pomocí impedanční defektoskopie s vyhotovením vlhkostní mapy
- Odběr sond ve zvolených místech
- Laboratorní vyhodnocení sond z hlediska složení střešního pláště, jeho celkové vlhkosti a laboratorní zkoušky fyzikálně-mechanických vlastností hydroizolační fólie
Uvedené první dva body jsou obvyklou rutinní záležitostí každého expertního posouzení ploché střechy.
Problematikou vlhkostního průzkumu pomocí impedanční defektoskopie a následným vyhotovením vlhkostní mapy se samostatně zabývá řada jiných článků např. [2].
Tento průzkum je bohužel velmi často zanedbáván, samozřejmě z důvodů nákladů na jeho provedení. Jeho výsledek však obvykle ukáže podstatně méně katastrofický stav, než jaký je běžně předpokládán. Tím může velmi přispět ke zpřesnění zadání pro projekt opravy nebo rekonstrukce a znamenat tak podstatné snížení nákladů. V případně zpracovaného projektu totiž projektant, který nemá dostatečné výchozí podklady, přistupuje z důvodů bezpečnosti k návrhu odstranění celého stávajícího střešního pláště a jeho nahrazení kompletní novou skladbou, což představuje obvykle velmi vysoké náklady.
Impedanční defektoskopií zjištěná vlhkost je pak konkrétně doložena odběrem sond a laboratorním stanovením vlhkosti v daných místech. Podle skutečně zjištěné vlhkosti lze sofistikovaným výpočtem a vhodnou metodikou predikovat dosažení rovnovážné vlhkosti stávajícího souvrství [3] a tím dát projektantovi jednoznačný podklad pro zpracování projektu bez nutnosti návrhu demontáže kompletního stávajícího souvrství.
3. Laboratorní zkoušky pro analýzu stávajícího stavu
Pro laboratorní zkoušky sloužící k určení fyzikálně-mechanických vlastností hydroizolační fólie odebrané ze sond na stávajících střechách nejsou předepsané normové postupy.
Jako vlastnosti nejlépe charakterizující stávající stav hydroizolační fólie lze považovat:
- stávající tloušťku fólie a její strukturu v řezu,
- ohebnost za nízkých teplot z projevu v řezu a na struktuře povrchu, které se vztahují k degradaci fólie a následně možné predikci její další životnosti a dále
- smykovou odolnost ve spojích,
- odolnost proti odlupování ve spojích,
které se vztahují k možnému provádění případných oprav a jejich funkčnosti a spolehlivosti.
Pro ověření těchto vlastností vycházím z norem pro zkoušení nových materiálů:
- ČSN EN 495-5. Hydroizolační pásy a fólie – Stanovení ohebnosti za nízkých teplot – Část 5: Plastové a pryžové pásy a fólie pro hydroizolaci střech. 2013.
- ČSN EN 12316-2. Hydroizolační pásy a fólie – Stanovení odolnosti proti odlupování ve spojích – Část 2: Plastové a pryžové pásy a fólie pro hydroizolaci střech. 2013.
- ČSN EN 12317-2. Hydroizolační pásy a fólie – Stanovení smykové odolnosti ve spojích – Část 2: Plastové a pryžové pásy a fólie pro hydroizolaci střech. 2010.
přičemž jak zkušební postupy, tak laboratorní zařízení jsou zjednodušené, ale prováděné tak, aby poskytly dostatečné informace potřebné pro zhodnocení stávajícího stavu a predikci jeho další životnosti a opravitelnosti. Laboratorní zkoušky provádím na vlastním necertifikovaném zařízení a zkoušky jsou provedeny na fólii odebrané ze sond a na nové originální fólii použité pro zapravení sond tak, aby bylo možné porovnat vlastnosti stávající i nové fólie a jejich vzájemnou svařitelnost.
4. Provedení zkoušek a vyhodnocení výsledků
Z odebraných sond jsou připravena zkušební tělesa pro všechny následující zkoušky.
Na tomto snímku jsou vzorky pro zkoušku ohebnosti za nízkých teplot a následně pro mikroskopické zkoumání. Pro stanovení ohebnosti za nízkých teplot je použita pouze jediná teplota, a to −18 °C a následné ověření chování fólie normovým způsobem stlačením zkušebního tělesa s posouzením vzniku trhlin na povrchu v rámci následné mikroskopické analýzy.
Při těchto provedených zkouškách lze vzhledem ke vzniku nebo nevzniku lomových trhlin posoudit ovlivnění jejich vlastností únikem měkčidel a následnou ztrátou jejich elasticity a tak posoudit původní kvalitu materiálů z hlediska surovin a přísad použitých pro výrobu.
U vzorků, u nichž nevzniknou lomové trhliny ani po jejich užívání po dobu 15–20 let, již nelze očekávat výraznější ztrátu měkčidel ze struktury a tedy ani ztrátu jejich vlastností a lze očekávat jejich další spolehlivou životnost. Jinak je tomu v případě projevu lomových trhlin, které by znamenají výraznou ztrátu fyzikálně-mechanických vlastností hydroizolační fólie a tedy možnost jejího poškození jakýmkoli mechanickým vlivem – pohyb osob po povrchu, krupobití apod.
Častým jevem je povrchová krakeláž (mikrotrhlinky), kterou však možno přisoudit spíše dlouhodobému působení povětrnostních vlivů než jednorázové zkoušce ohebnosti za nízkých teplot.
Po provedení zkoušky ohebnosti za chladu jsou pak vzorky podrobeny na řezu i na povrchu mikroskopickému zkoumání pomocí elektronického mikroskopu. Při zkoumání na řezu je posuzována homogenita, celková tloušťka a její případné kolísání, struktura a tloušťka jednotlivých vrstev a posuzuje se zejména celková tloušťka ve vztahu k původně deklarované – tedy úbytek celkové tloušťky za dobu užívání fólie – a tloušťka a stav UV odolné vrstvy jako dva rozhodující parametry pro posouzení stávajícího stavu fólie a možnou predikci jejího dalšího spolehlivého užívání.
Stanovení tloušťky fólie je provedeno jako součást mikroskopického průzkumu struktury fólie a to měřítkem, které je softwarově k dispozici.
Výsledky mikroskopického zkoumání jsou pak zřejmé z následujících mikrofotografií.
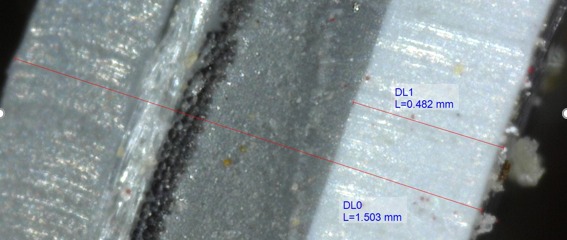
Obr. 2 Mikrosnímek řezu nové fólie použité pro opravy sond – je zřejmá korektní celková tloušťka i dobrá tloušťka UV odolné vrstvy jakož i homogenita struktury
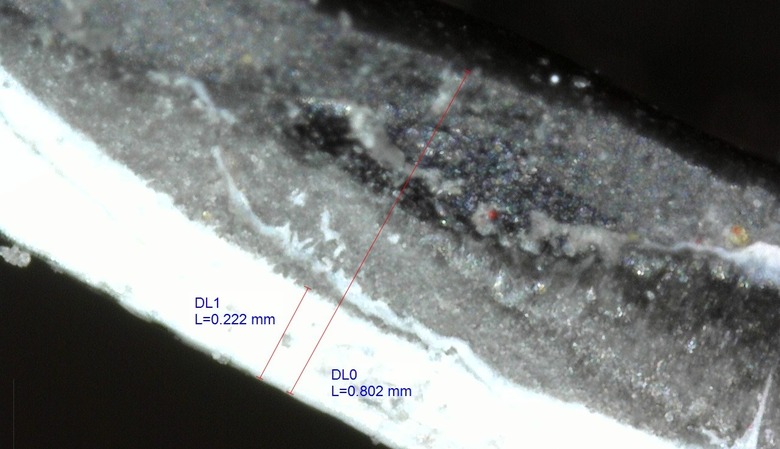
Obr. 3 Tento mikrosnímek dokumentuje stav fólie po cca 20 letech , kdy původně byla použita fólie tloušťky 1,2 mm. Současný stav pak znamená úbytek celkové tloušťky cca 30 % i kolísání tloušťky podél řezu při dostatečně zachovalé tloušťce UV odolné vrstvy.
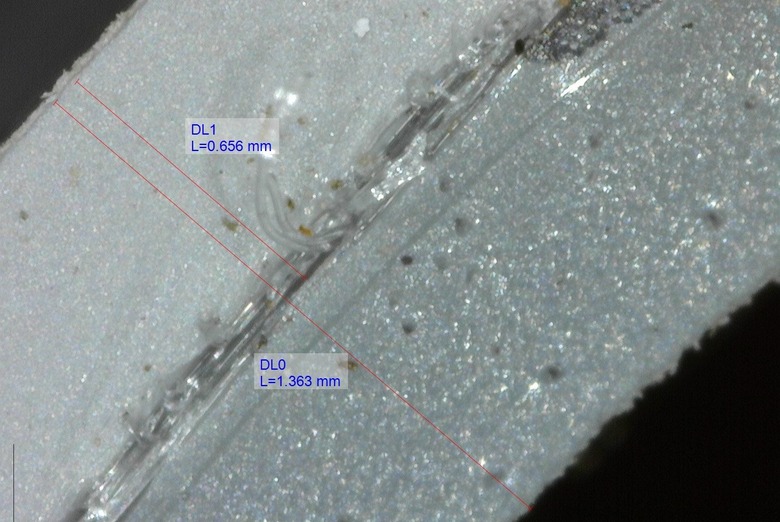
Obr. 4 Na tomto mikrosnímku je fólie původní tloušťky 1,5 mm po cca 15 letech užívání. Úbytek celkové tloušťky je cca 10 % a výrazně kvalitní tloušťka UV odolné vrstvy dokumentuje vysokou kvalitu použité fólie.
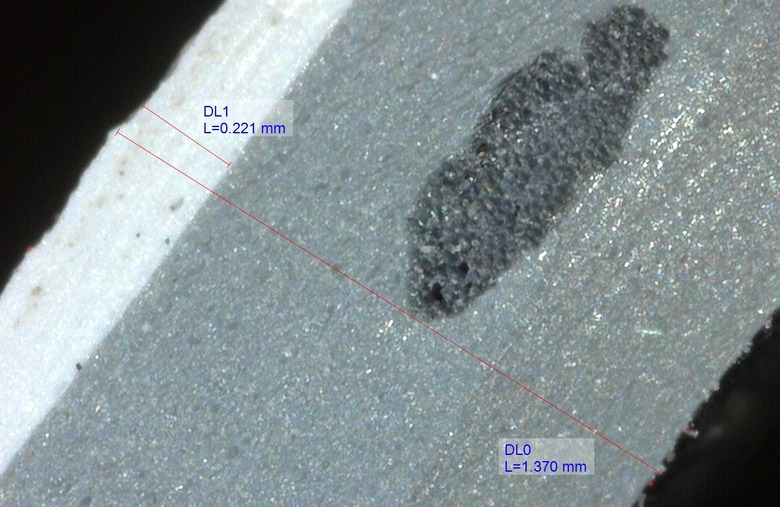
Obr. 5 Na tomto mikrosnímku je fólie ze stejného objektu jako u fólie výše, ale z jiné plochy. Celková tloušťka je obdobná, tloušťka UV odolné vrstvy je ale zhruba třetinová a je tedy zřejmé, že na této ploše byla použita fólie z jiné výroby nebo dodávky.
Následné mikrofotografie dokumentují stav zkoumání povrchu fólie po provedených zkouškách ohebnosti za chladu.
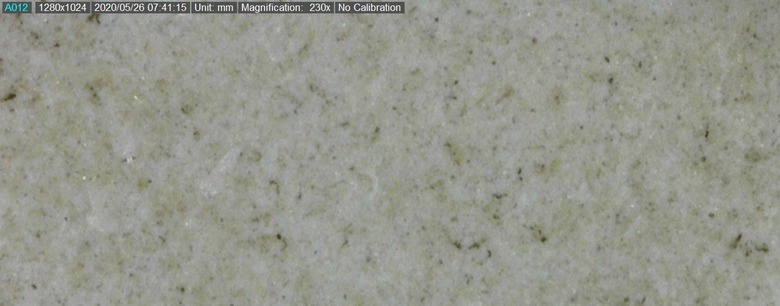
Obr. 7 Mikrofotografie povrchu fólie po cca 15leté expozici povětrnostním vlivům bez zřetelných problémů, jde o vzorek výše uvedené fólie s velmi kvalitní UV odolnou vrstvou
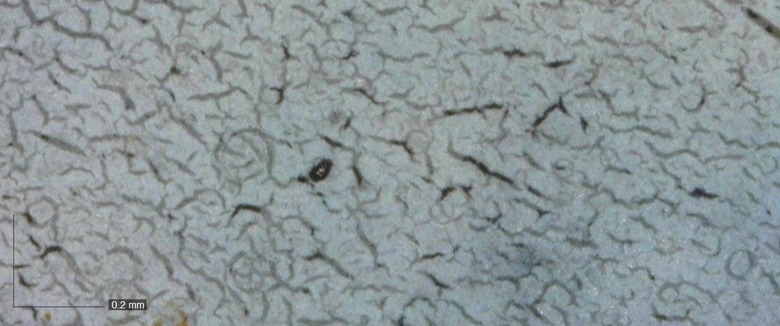
Obr. 8 Mikrofotografie povrchu fólie po cca 15leté expozici povětrnostním vlivům s výraznou krakeláží povrchu, ale bez projevu zlomových trhlin
Pro stanovení smykové odolnosti a odolnosti proti odlupování ve spojích je na vzorek původní fólie ze sondy nataven vzorek nové fólie samozřejmě po řádném očistění a technologicky korektním provedení. Pro zkoušku je pak používáno jednoduché mechanické zařízení bez možnosti stanovení konkrétní pevnostní hodnoty. To ale, na rozdíl od laboratorních zkoušek nových materiálů, není bezpodmínečně nutné, v tomto případě jde spíše o zjištění, jakým způsobem dojde k porušení ve spoji a z toho o určení opravitelnosti stávající fólie a funkčnosti a spolehlivosti takového opravného spoje.
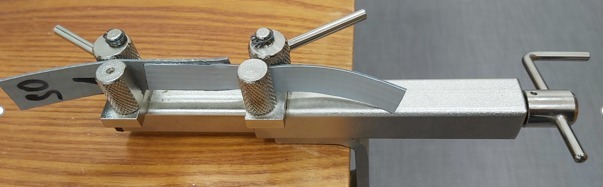
Obr. 9 Vložený vzorek pro stanovení smykové odolnosti ve spojích
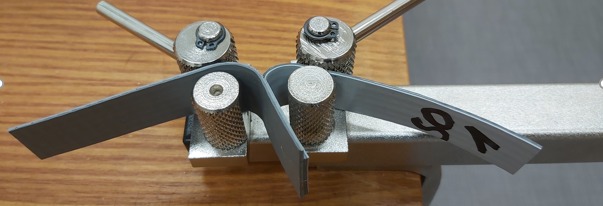
Obr. 10 Vložený vzorek pro stanovení odolnosti proti odlupování ve spojích
Výsledky těchto zkoušek dokumentují následné fotografie.
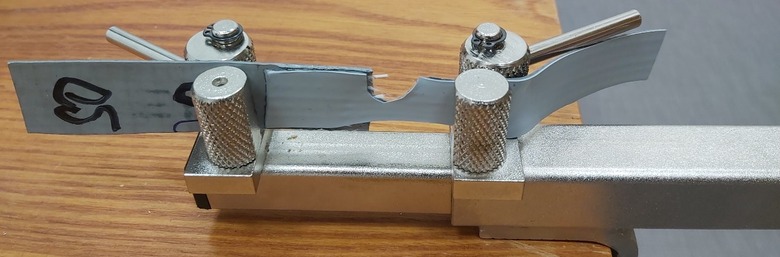
Obr. 11 Fotografie dokumentuje přetržení vzorku mimo oblast spoje, a to ve hmotě nové fólie. Spoj lze tedy z hlediska odolnosti ve smyku považovat za funkční a spolehlivý.
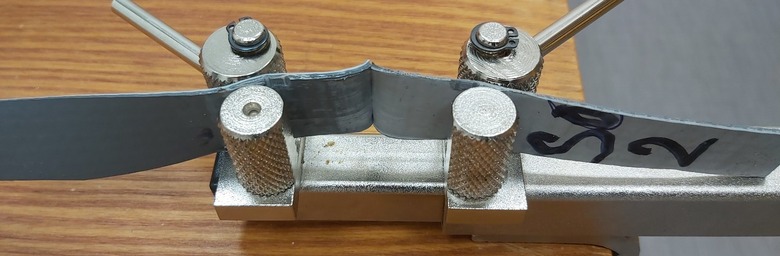
Obr. 12 Fotografie dokumentuje odloupnutí spoje stávající a nové fólie na vzájemném rozhraní jejich povrchů. Takový spoj, i když prokáže odolnost ve smyku, nelze považovat za dlouhodoběji spolehlivý.
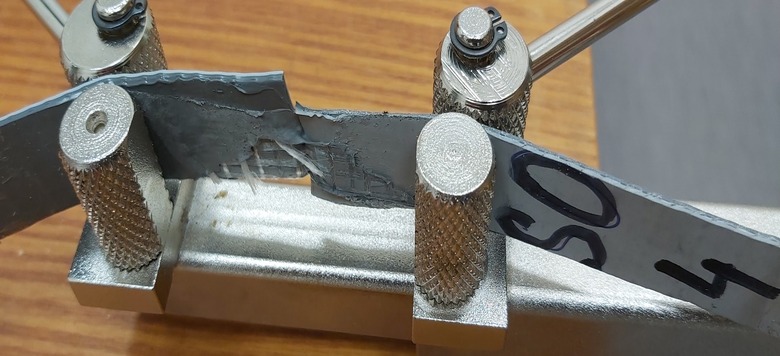
Obr. 13 Tato fotografie dokumentuje dva možné projevy odloupnutí ve spoji, a to buď na rozhraní povrchů, nebo odloupnutí ve hmotě některé fólie. Zde je odloupnutí ve hmotě patrné na části, kde hmota fólie se odloupla od vložky a lze z takového druhu odloupnutí odvozovat dokonalou spolehlivost a funkčnost spoje.
Je tedy zřejmé, že při posuzování vad a poruch stávajícího střešního pláště a zejména jeho hydroizolační vrstvy je vhodné neprovést pouze vizuální prohlídku a mechanické ověření stavu spojů, ale využít i laboratorních zkoušek, které celkový obraz stávajícího stavu jasně dokumentují.
5. Predikce další živostnosti na základě analýzy stávajícího stavu
Pro případ zájmu o predikci spolehlivosti oprav a možné další životnosti hydroizolační vrstvy jsou však laboratorní zkoušky jednoznačně nezbytné [4]. Pokud výsledky laboratorních zkoušek přinesou zjištění o úbytku celkové tloušťky větším než 30 %, vznik lomových trhlin při zkoušce ohebnosti za chladu a výrazné krakeláži povrchu, což se obvykle následně projeví i na zkouškách smykové odolnosti a odolnosti proti odlupování ve spojích, pak nelze predikovat spolehlivost další životnosti a je nutné doporučit její kompletní výměnu.
Pokud však laboratorní zkoušky přinesou výsledky úbytku celkové tloušťky fólie do 10 % při výborné tloušťce UV odolné vrstvy, bez vzniku lomových trhlin při zkoušce ohebnosti za chladu a dobrého stavu povrchu, což pak ještě potvrdí dobré výsledky zkoušek odolnosti spoje a to po cca 15 letech užívání, pak lze predikovat další spolehlivou životnost při zajištění průběžné kvalitní údržby a doporučitelném ověření stavu hydroizolační fólie po dalších 5 letech.
6. Závěr
Zájem uživatelů a majitelů o predikci další možné živostnosti střešního pláště i v případě odstranění vzniklých vad a poruch podstatně vzrůstá, protože obvyklá projekční praxe doporučující kompletní demontáž stávající skladby a nahrazení skladbou novou je záležitost finančně a mnohdy i provozně náročná.
Na základě kvalitního průzkumu střešního pláště a provedených laboratorních zkoušek materiálů v jeho skladbě, zejména hydroizolační vrstvy, je možno takovou predikci podložit jednoznačnými technickými argumenty.
I když se tento příspěvek zabývá posouzením stavu a vlastností hydroizolačních fólií po určité době užívání, mohu závěrem rozhodně doporučit laboratorní zkoušky nové fólie i v případě rozsáhlejších a náročnějších investičních projektů zejména pro určení kvality fólie z hlediska posouzení deklarovaných vlastností a vlastností materiálu skutečně na stavbu dodaného.
7. Literatura
- Technická komise pro hydroizolační fólie http://www.tkhif.cz/cs
- https://www.izolace.cz/clanky/zkusenosti-po-roce-zavedeni-impedancni-defektoskopie-a-mereni-vlhkosti-v-cr/
- TICHOMIROV, V. Predikce vývoje stavebně fyzikálních vlastností střešních plášťů plochých střech. Habilitační práce v oboru soudní inženýrství. Vysoké učení technické v Brně, Ústav soudního inženýrství. Brno, 2018.
- TICHOMIROV, V. Optimalizace technického řešení jako podpůrný prostředek při mediaci v obchodních sporech o vady a poruchy ve stavebnictví. Disertační práce. Ústav práva a právní vědy o.p.s. Praha, 2019.
In the expert business, the usual requirement is to find a possible fault, its cause and a proposal for how to eliminate it. More and more often, however, in expert practice I encounter the requirement to simultaneously assess the current state of the flat roof and especially the waterproofing layer and comment on its possible further functionality and durability.