Využití upravených tuhých odpadů z výroby minerální vlny do podlahových směsí
Příspěvek popisuje počáteční laboratorní návrhy, realizace a testování suchých podlahových směsí, ve kterých bylo snahou plnivo částečně či zcela nahradit upraveným tuhým odpadem z výroby minerální vlny – „granáliemi“. U návrhů požadavků na vyvíjené podlahové směsi a jejich složení bylo vycházeno z příslušných normových požadavků a z požadavků na běžně dostupné komerční směsi. Vyvíjená podlahová směs na cementové bázi musí být ve své finální realizaci vhodná k aplikaci jako vrstva vytápěné podlahy v občanské a bytové výstavbě, která není namáhána na obrus.
1. Úvod
Vlastnost samonivelační směsi | Hodnota |
---|---|
Pevnost v tlaku | 20 MPa |
Pevnost v tahu za ohybu | 4 MPa |
Obrusnost dle BCA | 0,040 mm |
Tekutost (rozlití kužele 100/70/60) | 230 až 250 mm |
Objemová hmotnost čerstvé směsi | 2000–2200 kg.m−3 |
Objemová hmotnost zatvrdlé směsi | 1800–2000 kg.m−3 |
Maximální zrnitost | 4 mm |
Hodnota pH | > 7 |
Teplotní roztažnost | cca 0,012 mm/m.K |
Součinitel tepelné vodivosti | min. 1,2 W/m.K |
Reakce na oheň | třída A1 (nehořlavý materiál) |
Doba zpracovatelnosti | max. 4 hod. |
Pochůznost | cca 24–48 hod. |
Částečná zátěž | cca 4–5 dní |
Vyvíjená samonivelační podlahová směs na cementové bázi musí být vhodná k aplikaci jako vrstva vytápěné podlahy v občanské a bytové výstavbě, které nejsou namáhané na obrus a musí vyhovět požadavkům normy ČSN EN 13813. Podmínkou při vývoji směsi je umožnění aplikace přímo na konstrukci teplovodního podlahového vytápění. Tato podlaha tedy musí mít ve své finální fázi velmi dobré flexibilní vlastnosti a samonivelační schopnost. Aplikace podlahové směsi by měla být prováděna litím při teplotách v rozmezí cca 5–30 °C. Tloušťka aplikované vrstvy podlahové směsi, by pak vzhledem k přítomnosti topných elementů ve skladbě podlahové konstrukce, měla být min. 50 mm, tak aby bylo zajištěno dostatečné překrytí topných těles. Nutným požadavkem je tedy i dobrá tepelná vodivost a tepelná roztažnost. Podlahová směs by rovněž měla vyhovět požadované třídě hořlavosti a doba zpracovatelnosti čerstvé směsi by neměla přesáhnout 4 hodiny. Samozřejmostí je i dostatečná únosnost zatvrdlé směsi v požadovaném časovém intervalu. V případě potřeby je předpokladem umožnění následné aplikace vhodné finální vyrovnávací stěrky na cementové bázi v tloušťce několika mm. Kritéria, stanovená na základě požadavků norem a obecných požadavků na dostupné komerční směsi, zobrazuje tabulka č. 1.
2. Odpad z výroby minerální vlny – granálie
U výrobců tepelných izolací, kde je vstupním materiálem minerální surovina na bázi křemičito-sodného sklovitého vlákna, vzniká odpad většinou ve formě neuspořádaných shluků sklovitého vlákna s různým obsahem vlhkosti na základě místa opuštění výrobně technologické linky případně způsobu uskladnění. Základní charakteristickou vlastností odpadů z výroby minerální izolační vlny je jejich minerální původ. Vzhledem k průběhu technologického zpracovaní, se jedná o pevný materiál rozdílné velikosti, tvaru a forem. Odpady z výroby minerální izolační vlny mohou obsahovat určité množství organických látek a vlhkosti na základě podmínek ukončení ve výrobním procesu.
Tyto odpady mohou vznikat v průběhu, ale většinou vznikají až na konci výrobního procesu. Tvorba tuhých odpadů z výroby minerální vlny probíhá již na počátku výrobní technologické linky, kdy se chladnější kapičky již nemohou protáhnout na vlákno a odletují od kotoučů jako drobná zrnka (tzv. granálie). Granálie (Obr. 1) z větší části padají do spodní části rozvlákňovacího stroje, kde jsou spolu s dalšími nerozvlákněnými podíly ukládány jako využitelný odpad, ke kterému se přidávají i odřezy a nestandardní podíly minerální vlny. Vznikají tak nesourodé odpadní materiály nehomogenních vlastností. Úpravou těchto tuhých odpadních materiálů na strojně-technologické lince vzniká zrnitý materiál – granálie. [1]
3. Vstupní analýzy
Na upravených granáliích bylo pro účely výzkumu nutné provést vstupní analýzy, které měli za úkol ověřit charakteristické vlastnosti tohoto strojně upraveného odpadu. Byla provedena série zkoušek, u kterých jsme se zaměřili převážně na stanovení technologických vlastností odebraných vzorků – celkového rozsahu zrnitosti (Obr. 2), sypných, měrných a objemových hmotností či na stanovení chemického složení. Pro ověření vlastnosti granálií i z ekologického a zdravotního hlediska bylo nutné provést stanovení obsahu kovů v sušině a vodném výluhu, stanovení obsahu přírodních radionuklidů či zkoušky ekotoxicity.
Obrázek č. 2 znázorňuje výsledky sítového rozboru a zastoupení jednotlivých frakcí v procentech. Z grafu je patrné, že hlavní zastoupení zrn v testovaném vzorku upravených granálií tvoří frakce v rozsahu 0,125 mm až 0,5 mm. Z granulometrického hlediska lze tedy granáliemi vhodně nahradit jemnozrnný písek ve směsi a vyhovují tak normovému požadavku na maximální velikost zrn ve směsi. Ostatní stanovené vybrané charakteristické vlastnosti granálií znázorňuje tabulka č. 2.
Stanovená vlastnost | Hodnota |
---|---|
Zrnitost | 0 až 2 mm |
Sypná hmotnost volně sypaná | 1419 kg.m−3 |
Sypná hmotnost setřesená | 1617 kg.m−3 |
Objemová hmotnost | 2500 kg.m−3 |
Hmotnostní aktivita Ra-226 | 27 Bq.kg−1 |
Měrná hmotnost | 2,786 g.cm−3 |
Měrný povrch | 31,6 m2.kg−1 |
4. Experimentální část
Hlavním záměrem experimentální části bylo ověření vhodnosti granálií jako částečné či úplné náhrady přírodního plniva v podlahové směsi. Pro tento účel byly navrženy zjednodušené receptury podlahových směsí, které na rozdíl od komerčně využívaných směsí obsahovaly podstatně nižší obsah jednotlivých složek, zejména chemických přísad ve svém složení. Tyto laboratorně navržené receptury sloužily pouze pro stanovení možného vlivu přídavků granálií na vlastnosti čerstvých směsí a k ověření jejich vlivu na pevnostní charakteristiky zkušebních vzorků zatvrdlých malt.
Během laboratorního ověřování byly nejdříve realizovány standardní receptury maltových směsí bez přídavku granálií. Tyto standardy nám sloužily ke stanovení počátečních hodnot, zejména fyzikálně mechanických vlastností a k následnému srovnání zjištěných hodnot u následných navržených receptur s obsahem granálií. Standartní receptura vyvíjeného produktu se skládala z pojiva – portlandského cementu pevnostní třídy 42,5 R a plniva – jemnozrnného křemičitého písku frakce 0–0,5 mm. Objem potřebné záměsové vody pro zpracování suché směsi byl stanoven dle požadovaného vodního součinitele a dle stanovených orientačních hodnot rozlití čerstvé směsi. U všech testovaných receptur byl dodržen konstantní vodní součinitel.
Poté bylo přistoupeno k přídavkům granálií do standardních směsí v rozsahu 50%, 75% a 100% náhrady plniva ve směsi. Za účelem obohacení směsi a vylepšení výsledných pevností zatvrdlých zkušebních těles po 7 a 28 dnech byla do směsi rovněž přidávána prášková disperze Vinnapas.
Po navážce jednotlivých surovin byla suchá směs promíchána v laboratorním homogenizátoru a po přídavku potřebného množství vody byla směs míchána po dobu 4 minut v laboratorním mísícím zařízení. Čerstvá směs byla podrobena zkoušce konzistence a byla stanovena objemová hmotnost čerstvé směsi a následně byla tato směs uložena do forem pro výrobu standardních zkušebních těles o rozměru 40×40×160 mm.
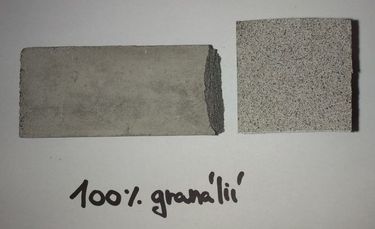
Obr. 3: Zkušební těleso 40×40×160 mm se 100% náhradou plniva granáliemi po zkoušce pevnosti v tahu ohybem
Laboratorně vyrobená zkušební tělesa podlahových směsí byla následně testována dle požadavků normy ČSN EN 13813 – Potěrové materiály a podlahové potěry. Tato evropská norma určuje požadavky na vlastnosti čerstvých a zatvrdlých potěrových materiálů, jejichž pojivovými složkami jsou cement, síran vápenatý, hořečnaté pojivo, asfalt a pryskyřice. Uvádí jejich třídění a požadavky na vlastnosti z nichž normativní jsou pevnosti v tlaku a v tahu za ohybu. Volitelná jsou pak stanovení odolnosti proti obrusu, tvrdosti povrchu smrštění a rozpínání a další fyzikální a mechanické vlastnosti, příchází-li v úvahu. [2]
Na obrázku č. 3 můžeme sledovat rozptýlení jednotlivých zrn granálií (černé body) v průřezu zkušebního tělesa. Jak je patrné došlo k pravidelnému rozptýlení jednotlivých zrn granálií po celém objemu zkušebního vzorku a nedocházelo tak k jejich usazování ve spodní části. A to i přesto, že bylo pozorováno mírné vzlínání záměsové vody na povrchu těles, po odlití čerstvé směsi do forem. Toto vzlínání bylo pravděpodobně způsobeno výškou formy 40 mm, která je větší než předpokládaná výška jedné aplikované vrstvy samonivelační podlahy a mírným nadbytkem použité záměsové vody.
Srovnání objemových hmotností testovaných vzorků po 7 dnech zrání vzorků zobrazuje obrázek č. 4. Výsledné pevnosti v tlaku a v tahu za ohybu po 7 dnech zrání vzorků a jejich vzájemné srovnání vystihuje obrázek č. 5.
Graf na obrázku č. 4 zobrazuje srovnání objemových hmotností jednotlivých zkušebních těles s různým obsahem granálií ve směsi. Granáliemi byl nahrazován jemnozrnný písek ve směsi, a to v rozsahu 0%–100% hmotnosti plniva. Z grafu je patrné, že společně s nárůstem obsahu granálií ve směsi mírně vzrostla i objemová hmotnost zkušebních těles. Jelikož se jednalo o hodnoty získané z měření zkušebních těles po sedmi dnech zrání, byly předpokládány další změny těchto hodnot v průběhu zrání zkušebních těles. Z hlediska stanoveného rozsahu objemové hmotnosti po 7 dnech zrání zkušební tělesa vyhověla, a to až do 100% náhrady plniva granáliemi.
Graf na obrázku č. 5 znázorňuje výsledky měření hodnot pevností v tlaku a v tahu za ohybu po 7 dnech zrání zkušebních těles. Z grafu je patrné, že vlivem náhrady přírodního kameniva granáliemi dochází od hodnoty 50 % k mírnému poklesu hodnot pevností v tlaku i v tahu za ohybu. Naopak u směsi s 25% náhradou plniva granáliemi došlo k mírným nárůstům pevností oproti standardu, a to jak pevností v tlaku, tak i pevností v tahu za ohybu. Výsledné pevnosti zkušebních těles po 28 dnech zrání popisuje graf na obrázku č. 7.
Jak je z grafu na obrázku č. 6 patrné, objemové hmotnosti po 28 dnech zrání vzorků měly vzrůstající tendenci v závislosti na zvyšujícím se obsahu granálií ve směsi. Všechna zkušební tělesa vyhověla stanovenému rozsahu objemové hmotnosti 1800 kg/m3 až 2000 kg/m3, a to i v případě 100% náhrady plniva granáliemi. Proto lze tento výsledek pokládat za vyhovující.
Graf na obrázku č. 7 zobrazuje srovnání pevností v tahu za ohybu a v tlaku naměřených na zkušebních tělesech po 28 dnech zrání v laboratorním uložení. Můžeme pozorovat, že vlivem zvyšujícího se obsahu granálií ve směsi dochází k nárůstu výsledných pevností zkušebních těles v tlaku i v tahu za ohybu, ovšem opět pouze do hodnoty 50% náhrady přírodního plniva granáliemi. V případě pevností v tahu za ohybu bylo u všech zkušebních těles dosaženo požadované pevnosti 4 MPa. Z tohoto hlediska lze tedy všechny odzkoušené receptury považovat za vyhovující. V případě pevností v tlaku bylo dosaženo požadovaných 20 MPa pouze u dvou testovaných receptur s obsahem granálií 25 % a 50 %. Nutno však podotknout, že referenční receptura bez obsahu granálií hodnoty pevnosti v tlaku 20 MPa rovněž nedosáhla.
5. Závěr
Dosavadní laboratorní práce prokázaly, že z hlediska zkoušených pevnostních charakteristik zkušebních těles je možné částečně či zcela nahradit přírodní plnivo v testované podlahové směsi odseparovanými a upravenými granáliemi z výroby minerální vlny.
V případě většiny zkušebních vzorků došlo ke splnění požadavků na stanovenou hodnotu objemových hmotností i pevností v tlaku i v tahu za ohybu. Pouze v případě pevností v tlaku zkušební vzorky nedosahovaly ve všech případech požadované hodnoty 20 MPa. Jedná se však o počáteční návrhy receptur, které ve svém vývoji budou dále modifikovány o další složky a přísady, lze proto předpokládat další navýšení hodnot pevností zkušebních těles.
V následujících fázích vývoje plánujeme rozšíření receptur navržených směsí o další složky. Jemnozrnné plnivo v podobě písku a granálií bude, za účelem zlepšení zejména reologických vlastností čerstvé směsi, doplněno o mikro-mletý vápenec. Pojivová složka v podobě portlandského cementu bude rozšířena o přídavek hlinitanového cementu, tak aby byl zajištěn rychlejší nárůst počátečních pevností. Stejně tak zvažujeme využití portlandského cementu vyšší pevnostní třídy. Navržené receptury budou rovněž rozšířeny o další chemické přísady. Vlivem přídavku hlinitanového cementu do směsi bude nutné recepturu rozšířit o retardér či urychlovač tuhnutí hlinitanového cementu, dále bude navržená směs doplněna o přídavky dalších chemických přísad v podobě práškového plastifikátoru či etheru celulózy, tak aby se výsledné vlastnosti laboratorně navržené podlahové směsi co nejvíce přiblížily vlastnostem komerčně vyráběných podlahových směsí a aby tak byly splněny veškeré kritéria a požadavky, které jsou na moderní podlahové směsi kladeny.
Tento článek byl vytvořen za finanční podpory Technologické agentury ČR v rámci řešení projektu TA 02021147 – Výzkum a vývoj optimálních environmentálně šetrných technologií pro nové a progresivní využití tuhých odpadních materiálů z výroby minerální vlny.
Literatura
- [1] LEBER P. Odborná zpráva o postupu prací a dosažených výsledcích. Brno, 2012. Roční/dílčí zpráva projektu: TA02021147. Výzkumný ústav stavebních hmot, a.s.
- [2] ČSN EN 13813. Potěrové materiály a podlahové potěry – Potěrové materiály – Vlastnosti a požadavky. Praha: Český normalizační institut, listopad 2003. 28 s.